Staad Pro V8i Ss6 Technical Reference Manual
- Staad Pro V8i Ss6 Technical Reference Manual Pdf
- Staad Pro V8i Ss6 Technical Reference Manual Rapid Overview
- Staad Pro V8i Ss6 Technical Reference Manual User
JavaScript must be enabled in order to use this site.
Please enable JavaScript in your browser and refresh the page.
(A) Issues addressed in the Analysis/Design engine (100)
Read PDF Technical Reference Manual Staad Pro V8i Technical Reference Manual Staad Pro V8i OpenLibrary is a not for profit and an open source website that allows to get access to obsolete books from the internet archive and even get information on nearly any book that has been written. V20.07.11.9 2 Comments / Civil Architecture All General Softwares, Civil Books Platform / By admin STAAD.Pro V8i SELECTseries half dozen (20.07.11.33) introduces the most recent enhancements to the world’s leading analysis and style application.
A) 01 The calculation to determine the natural torsion for rigid floor diaphragms with the IS 1893 response spectrum analysis has been corrected. The effect was being calculated based on values of alpha and delta and about the centre of rigidity, instead of using factors of (alpha-1) and (beta-1) and applying the force about the centre of mass. This resulted in over estimating the torsional forces and thus conservative results.
Download and install most demanded Structuralal analysis and design Software STAAD PRO V8i SS6, with Free Begineers Exercise. STAAD.Pro v8i Select Series 6 - Technical Reference Manual.
A) 02 The calculation to determine the natural torsion for rigid floor diaphragms with the seismic equivalent static method for IS 1893 has been corrected. The effect was being calculated based on values of alpha and delta and about the centre of rigidity, instead of using factors of (alpha-1) and (beta-1) and applying the force about the centre of mass. This resulted in over estimating the torsional forces and thus conservative results.
A) 03 The IS 1893 seismic load generation has been updated to ensure that the details of the applied moments about origin due to seismic load are reported correctly with the presence of rigid diaphragm as the torsion increases the moment (i.e. MY). Even though this increase in moment is considered in analysis, this was not considered while reporting the moment MY about origin.
A) 04 The RIGID DIAPHRAGM was corrected in the SS5 release to ensure that when this was used with a CHANGE command, the additional results were not getting added correctly. It was subsequently found that under certain circumstances this correction was not being implemented. This loophole has been corrected.
A) 05 The IS 1893 Response Spectrum analysis specification has been corrected to include the natural / inherent torsion, generated due to the difference between CM and CR when dynamic loading is acting along Z direction, which was not getting added to the original load vector.
A) 06 The Eurocode EN 1993-1-1 steel design routines for calculating the properties of Class 4 slender, Tee sections has been corrected to ensure that when multiple such sections are designed the second and subsequent sections used the appropriate section properties.
A) 07 The ASME NF 3000 2004 code has been updated to correct design of single angles that have been collated in a group.
A) 08 The AISC 360-05 and AISC 360-10 design codes have been updated to correct the design of Tee sections ensuring that the value of Cy is calculated correctly.
A) 09 The analysis engine has been updated to ensure that when processing a PMEMBER command which includes a list of non existent members (say 1 TO 1000, where only 1 and 1000 have actually been defined), only the members that actually exist will be assigned as part of the PMEMBER. Previously an assignment list of 1 TO 1000 would represent 1000 segment parts to the PMEMEBER and thus reported as an error.
A) 10 The Russian steel design modules have been updated to ensure that all necessary variable are correctly initialised which was causing the design to crash.
A) 11 The analysis has been updated for loading on models with physical members. If a concentrated force is applied to a PMEMBER specified with an eccentricity using the D2 parameter, then the eccentricity is included in the analysis.
A) 12 A new test has been introduced in the analysis when analysing a model with the IS 1893 seismic specification to ensure that the base dimension is not zero (such as with a simple single line stick model representing a chimney or tower) and the commands includes the ST parameter. This would result in a divide by zero error, thus a warning message is reported and the analysis halted.
A) 13 The design of sections to EN 1993-1-1 that have been classified as class 3 and subject to high shear loading have been updated to ensure that the interaction ratio reported is based on the reduced bending capacity.
A) 14 The Russian steel design modules have been updated for checking when Mef>30 and a correction introduced for the value of PhiB
A) 15 The principal that when working with dynamic load cases, the mass matrix is determined from the first dynamic load case. This was inadvertently changed in the SS5 release and has been reverted to the original philosophy and now an additional NOTE is included in the output file to indicate the load case from which the mass matrix has been determined.
Staad Pro V8i Ss6 Technical Reference Manual Pdf
A) 16 The provision of RIGID FLOOR DIAPHRAGM was not allowed for when including compression/tension only support springs, elastic and plate mat foundations. The addition of nodes for the rigid diaphragm was not being accounted for and would result in an error in the analysis. This has now been addressed.
A) 17 The BS5950 steel design module has been updated to ensure that composite members are excluded from the design as these are outside the scope of the design module.
A) 18 The AISC 360 design of tube sections has been updated to ensure that if the torsional modulus C has not been provided, then it should use C = 2(B-tw)(H-tf)t - 4.5(4-pi)t^3. However the calculation was not including the wall thickness and hence over estimated the torsional modulus.
A) 19 A new SET option has been added to improve the ability for floor loads to be defined on inclined surfaces. SET FLOOR ANGLE TOLERANCE (which has a default of 0.01 degrees) can be used to determine the selection of nodes that will be included in a FLOOR LOAD command.
A) 20 The ACI 318 concrete design routines for plate elements have been updated to ensure that only the required steel as per clause 7.12.2.1 is provided.
A) 21 The South African steel design SABS0162-1:1993 output has been updated to ensure that the header for a TRACK 2 output is only printed once.
A) 22 The ACI 318-11 concrete column design routine has been updated to include the moment magnification method as outlined in clause 10.10.5
A) 23 The Eurocode design has been updated to include additional SGR parameter options to cover all 32 steel grades and updated Table 6.1 and 6.2 to define appropriate buckling curves.
A) 24 The AIJ steel design code has been update to allow a reduced effective section modulus determined from the flanges only to be used in the design of wide flange and channel sections.
A) 25 The advanced analysis engine has been completely reformatted with new routines to provide even faster methods to build and solve the stiffness matrix.
A) 26 The AS 4100 steel design routine has been updated to ensure that tapered wide flange sections are correctly handled.
Staad Pro V8i Ss6 Technical Reference Manual Rapid Overview
A) 27 The track 1 output for an EN 1993-1-1 design has been updated to remove an unnecessary blank line in the header which will help readability and consistency with other similar design code headers.
A) 28 The ACI 318-11 concrete design routines have been added. The fundamentals remain consistent with the previous 318-08 code, but include the addition of the moment magnification method.
A) 29 The South African standard SANS 0162-1:2011 has been added to STAAD.Pro for the design of steel members.
A) 30 The Japanese Steel design codes AIJ 2002 and AIJ 2005 have been enhanced with an additional option on the Von Mises checks to perform the check, but exclude the torsion stresses which is required by various plant deign specifications.
A) 31 The detailed output from an AISC 360-10 design has been updated such that if the LTB checks are not appropriate to the design, the values of Lb, Lp and Lr will not be included in the report.
A) 32 The Japanese steel design code AIJ 2002 has been enhanced with an additional parameter 'YNG' which allows the calculation of fb (eqn 5.8) to change from fb =8900/(Lb*h/Af)(the default method) to fb=0.433*E/(Lb*h/Af), where E is taken as the defined value of Young's Modulus as published by the JSME Eqn SSB-1.10.
A) 33 The AISC 360-10 and AISC 360-05 design codes have been enhanced to support the design of members with tapered flanges.
A) 34 The seismic load routines have been supplemented with the specification for IBC 2012 / ASCE 2010.
A) 35 The AISC 360-10 design report has been updated to give the exact equation for each category of PhiPn.
A) 36 The AISC 360-10 summary output for a TRACK 0 setting has been rationalised to reduce the amount of unnecessary data printed and making for a more compact report.
A) 37 The Advanced Analysis engine has been enhanced with an additional method to extract the dynamic modes using a Ritz Vector method.
A) 38 The AISC 360-05 and AISC 360-10 codes have both been updated to allow the output reports to be provided in the current length and force units, so can now be provided in metric and not just English units.
A) 39 The ACI 318 concrete design routines for T shaped beams was modified in the SS5 release to ensure that if the dimensions of the web and the moment on the section are such that a suitable area of bars can be determined (i.e. between Rhomax and Rhomin), then that arrangement is now reported.
A) 40 The AISC 360-05 and AISC 360-10 codes have been updated to support the design of wide flange sections with cover plates on the top and/or bottom flanges.
A) 41 The AISC 360-10 and AISC 360-05 design modules have been enhanced with an option to include the additional checks as per the corresponding AISC 341 specification 'Seismic Provisions for Structural Buildings'
A) 42 The dynamic analysis routines have been improved when creating the mass matrix that needs to be saved to disk after completing the eigensolution. With the V8i SS5 release this would result in the analysis aborting during this process due to an IO error.
A) 43 The AISC 360-10 TRACK 2 report has been updated to include the torsional modulus (Ixx) that is being used in the design. Also when wide flange sections are modified with cover plates on both the top and bottom, the values of torsional modulus (Ixx) and warping constant (Cw) are modified to enhance the torsional characteristics that the plates provide.

A) 44 The AISC 360 TRACK 2 output has been revised to indicate the units of the values being reported in the header with any that are not in those units having their own unit indicated in that section of the output.
A) 45 The analysis engine has been updated to ensure that if a list command such as DELETE or INACTIVE MEMBER with a FROM … TO … STEP … is defined such that (TO-FROM)/STEP is not an integer, then this is reported as an error.
A) 46 The Canadian steel design CSA S16-14 has been added to the range of available steel design codes.
A) 47 The output from an AISC 360 10 has been updated to correct the value of Azz that was being reported. However, the value that was being used in the calculations was correct.
A) 48 This is a note to confirm that AISC 360 clause H3-8, non-HSS sections subject to combined shear and torsional forces, was corrected in release 20.07.09.31, but not documented in that release. This accounts for members whose shear centre and centroid do not coincide, resulting in an torsional effect on the member.
A) 49 The design of angle sections to AISC 360-05 and AISC 360-10 has been improved. The report had previously inverted the values of IY and IZ displayed and the slenderness calculations had inverted the slenderness factors KY and KZ.
A) 50 The AISC 360 05 and 10 design routines have been enhanced with a new INT parameter which allows the selection of interaction checks H1-1 and H1-3, the default INT 0 performs exactly as per earlier releases of STAAD.Pro.
A) 51 The AISC 360-10 design of pipe and HSS round sections has been updated to better handle forces in orthogonal directions. These forces are now resolved into a single direction as recommended by the AISC committee and defined by Mr = sqrt(MY*MY + MZ*MZ) for use in equations such as H3-6.
A) 52 The IBC 2006/2009 response spectrum routines have been enhanced with the ability to include the torsional effects as done in the Indian IS 1893 code using the two parameters DEC and ECC to account for the difference between the centre of mass and the centre of rigidity.
A) 53 The IS 456 concrete design routine has been enhanced with a check on the value of Young's modulus specified for the concrete which is reported if an inappropriate value is used. Previously a warning reported excessively high values >10,000 ksi. Now an additional test checks to prevent using a value of E <100 ksi.
A) 54 The analysis engine has been updated to improve the handling of Notional load cases which under certain conditions would cause the analysis engine to generate a run-time error.
A) 55 The analysis engine has been updated to include a new and wider set of properties for models that include the ASSIGN BEAM, COLUMN, CHANNEL or ANGLE specification to select a profile from the current database where that is appropriate.
A) 56 The EN 1993-1-1 steel design has corrected the calculation of the warping constant for channel sections. Previously this could generate negative values, although the correct magnitude, which when used would result in an incorrect utilization value which could be non-conservative or report as not a number, i.e. nan.
A) 57 The South African steel design code SANS0162-1:1993 has been updated to correct the design of T section profiles to ensure that the value of MR is calculated and MRZ as per section 13.5 and 13.6.
A) 58 The South African steel design SABS0162-1:1993 has been updated to ensure that the effective length factors KY and KZ are used in the determination of the compression capacity.
A) 59 The IS800:2007 design of web tapered members has been improved to ensure that if the section is subject to tension, the compression capacity is still calculated and reported correctly.
A) 60 The IS800:2007 steel design has been improved for members defined as truss members and web tapered where previously the slenderness ratio was reported as 0.0, this is now calculated and reported correctly.
A) 61 The IS800:2007 design of UPT sections has been improved taking into account the area specified in AX rather than determining the value from the section dimensions.
A) 62 The SNiP 2.23-81 Russian steel design code has been updated to ensure that the units of yield stress are correctly taken into account.
A) 63 The AISC 360 design routines have been modified to improve the design of Tee profiles to check for the condition of Iyc/Iy. For sections for which Iyc/Iy is between 0.1 and 0.9, then their interaction will be determined from clause H2 rather than H1.
A) 64 The Russian steel design code SNiP 2.23-81 has been updated to ensure that the stability check is not performed where it has a relative eccentricity >20 (i.e. mef > 20).
A) 65 The AISC 360 steel design modules have been enhanced with the implementation of clause E5, compression capacity of single angles. This calculates the slenderness from equations 16.1-35 and 16.1-36, rather than directly from K, L and r.
A) 66 The AISC 360 steel design modules have been modified to ensure that clause E4 is only used where b/t > 20.
A) 67 The design of steel profiles to the older Russian steel SNiP II-23-81 has been revised to be initialised by the command CODE RUSSIAN 1990 and the output heading revised to report 1990 rather than 1998.
A) 68 The Canadian steel design S16-09 has been updated with an improved algorithm to increase the speed the design process.
A) 69 The Indian steel design IS 800:2007 has been updated with an improved algorithm to increase the speed the design process.
A) 70 The value of Ix used for a tapered I section for an Australian steel design AS4100 is now calculated and reported. Previously this was set as 0.0 and thus resulted in a design ratio of infinity.
A) 71 Designs using the following codes:- AISC 360-10, AISC 360-05, IS800:2007, Canadian S16-09 and Canadian S16-14 now support the use of ENVELOPE definitions to determine load cases which will be used for serviceability checks and which will be used for strength checks when performing member designs. E.g.
Will perform a design for load cases 101 to 210 and 201 to 210 where load cases 101 to 110 will be considered for the strength checks and load cases and 201 to 210 will be used for serviceability checks.
A) 72 The old Eurocode concrete design based on the draft for development publication has been removed from the analysis engine. The current Eurocode 2 EN1992-1-1 design should be performed from the Concrete Mode.
A) 73 The AISC 360 steel design modules have been updated to ensure that for fabricated sections (i.e. STP 2), the design includes the check for clauses E7-7 to E7-9.
A) 74 The old Eurocode 3 Draft for Development design code has been archived as all designs should adopt the current EN1993-1-1 methods.
A) 75 The analysis engine has been updated to correct the section forces reported on members that have been loaded with a combination case of static and response spectrum cases. Also when using the command to create a combination of an earlier defined combination which was of an ABS or SRSS type.
A) 76 The analysis engine has been updated to support the assignment of a time history forcing function to a node group definition which previously would cause the analysis engine to crash.
A) 77 The one way floor loading command has been updated to ensure that it is included in a Reference Load Case, if the option INLCLINED is included, that option is accounted for in the load distribution.
A) 78 The Russian steel design code SP16 has been updated to ensure that the values of Mef and thus Phi_e are correctly calculated for all members in a design collection. Previously whilst the first member in the design would be correctly calculated, the second and subsequent members may not be correct.
A) 79 The Eurocode 3 steel design EN 1993-1-1 has been updated to ensure that it does not crash when set to using the French National Annex, NA4.
A) 80 The Russian steel design SP 16 has been updated to correct the design of double angle profiles to ensure that the correct area of the composite profile is used and correcting the the values of Hef and Bef which resulted in incorrect values for Lamda_UW.
A) 81 A new CB parameter has been added to the Canadian steel design modules S16-09 and S16-14 to allow a user specified value of Omega2 as was supported in the earlier S16-01 design code.
A) 82 (The IS 800:2007 LSD and WSD have been updated to ensure that the design of tapered wide flange sections do not include the section classification limit as a design criteria which could result in a conservative over estimate of the design ratio.
A) 83 The Russian steel design codes have been updated to manage better the assignment of steel grades defined with SGR and MAIN parameters. If an inappropriate assignment is made such as a rolled steel grade assigned to a hollow profile, the design for that section is terminated.
A) 84 The detail output of the Russian steel design code SP16.13330 has been updated to clarify the eqn previously listed as 116 is in fact 117 (which is used in eqn 116 and the result reported in clause 9.2.9.
A) 85 The AISC 360-05 and 360-10 Unified design codes have been updated to correct the designs performed on models specified with the SET Z UP option in which previously the parameters such as K and L were being assigned to the wrong axis.
A) 86 The AISC 360-05 and AISC 360-10 design modules have been updated to include the parameter WTYP. This is used to indicate the method of fabrication of an HSS profile.
A) 87 The AISC 360-10 torsion design has been modified such that at this time TRACK 3 is not supported and a TRACK 2 report will be generated instead.
A) 88 The AISC ASD, 9th Edition has been updated to correct a recently introduced issue that resulted in the values of CY and CZ for channels and tees were not getting updated for the second and subsequent members in a group design.
A) 89 The AISC 360-05 and AISC 360-10 design codes have been updated to include the LEG parameter which is used to indicate which leg of an angle profile has been fixed in order to determine which radius of gyration should be used for the slenderness calculations.
A) 90 The AISC 360-05 and AISC 360-10 design code have been updated to ensure that the moments reported in the output for an angle profile design were for the correct axes. Note however that the design itself used the moments about the correct axes.
A) 91 The Norsok steel member design routine has been updated to ensure that where the critical design ratio is as a result of Eq. 6.44, this reference is displayed. Previously, some members could report the reference as Eq. 6.15 which is simply one of the parts that determine the final ratio. Note however, that the ratio reported was correct.
A) 92 The output for IBC 2006 and IBC 2012 seismic definitions has been updated to ensure that the value of CT reported in the output file as per the current unit system.
A) 93 In STAAD.Pro V8i SS5 20.07.10.64 a modification was added that attempted to assist in the analysis of models with warped plates (see A)78 of that Revision History document). The analysis would modify the stiffness of the warped plates in order to account for the warped nature of the plate. This modification has been removed so that the behaviour of STAAD.Pro will be as for earlier builds of STAAD.Pro. It is highly recommended that models with quad plates should be checked carefully for any warped plates and make use of the SET PLATE FLATNESS TOLERANCE command.
A) 94 The AISC 360 design code routines have been further optimised to improve memory utilization which on some larger models would cause the design cease.
A) 95 The wind loading defined with a Russian SNiP 2011 setting was failing to create any loading on some asymmetric building frames. Note that this uses a combined effect of the static force from the wind and dynamic effects of the structure, hence can result in asymmetric load and forces applied to a symmetrical structure. Also at this time a statics check will be reported, but this does not apply and will be removed in a future release.
A) 96 STAAD.Pro does not support multiple time history or ground motion load cases in a single run, but it is possible to have a case which is re analysed after a change such as when section profiles have been modified after a design. Whilst this was possible for time history cases, it was being prevented if the re analysed case included ground motion. This restriction has now been removed.
A) 97 A new Russian concrete design module has been added to allow design of concrete members to the Russian design code SP 63.13330.2012. This code supersedes the SP 52 design code that is currently available in the Concrete Design mode.
Staad Pro V8i Ss6 Technical Reference Manual User
A) 98 The error message reported by the analysis engine has been updated to clarify the nature of the problem when the required code is not included in the CHECK SOFT STORY (CODE) command as defined in the Technical Reference manual section 5.28.2 Floor Diaphragm.
A) 99 The output that is reported using a PRINT SECTION FORCE command has been updated to include the axial forces at the section locations.
A) 100 The processing of the IS1893 response spectrum command has been updated to support the ABS combination method which previously would have caused an error the analysis to abort.
(B) Issues addressed in the Pre-Processing Mode (30)
B) 01 A new Japanese steel design database has been added to support all the H sections defined in the AIJ 2014 publication.
B) 02 The toolbars have been updated to ensure that the status of their visibility is recorded and that they are displayed with the same status when the program is relaunched. So if a toolbar is turned off in one session, the next time the program is launched, the toolbar remains turned off, but can be turned on again from the menu item View>Toolbars...
B) 03 The Output Viewer has been updated to ensure that if any output file (*.ANL) is double clicked, it opens and is displayed in the viewer. Previously this would cause the Viewer to crash.
B) 04 The old Japanese steel database of H sections has been updated. The IZ value of the H346x174x6 profile has been corrected.
B) 05 The GUI has been updated to process the command line DEFINE IS 1893 LOAD which includes the parameter PART4, but where a space has been incorrectly introduced between PART and 4. This will be reported as an error rather than simply removed when the file is re-saved.
B) 06 The menu in the Modelling Mode that displays section properties for a selected country has been updated for the European steel database which previously was not including the rectangular, square and circular hollow section tables.
B) 07 The GUI has been updated to process PRINT SECTION FORCE commands that have list defined after the command as meaning ALL, i.e. this is treated as PRINT SECTION FORCE ALL rather than identifying this as an error.
B) 08 Sample STD files for the Verification Examples as outlined in section 'Steel-AISC LRFD' have been added to the installation.
B) 09 The US steel database has been updated to the publication from the AISC v14.1. Note however that the publication does not include B Shapes or Tubes, but these have been retained for information. Also the additional shapes, Heavy W-Shapes Large L Shapes and Jumbo HSS have been added.
B) 10 The Modes bar and menu has been updated to help in navigation.
B) 11 The Properties dialog box has been updated to improve the editing of user defined pipe and tube sections. If a profile has been defined with specified OD and ID dimensions, then if the section is edited, those defined dimensions will now be displayed in the edit window.
B) 12 The dialog for entering details of a 2-D orthotropic material has been updated to allow entry of the three orthogonal shear moduli.
B) 13 The old STAAD.Pro Editor has been provided for users who wish to continue using this tool, but has been updated to improve handling the syntax check routine that is run when the 'f5' key is pressed or the option selected from the tools menu.
B) 14 The European cold formed RHS and SHS section names have been updated removing an unnecessary dimension in the name.
B) 15 The GUI has been updated to support different character sets in a number of places including the recent file list on the Start Page, the file name in the STAAD analysis engine dialog and message list, The STAAD Output Viewer and the legacy Editor.
B) 16 The Member Query dialog box has been updated to ensure that the inertia properties of an angle arranged in a star formation is reported correctly.
B) 17 The GUI has been updated to ensure that if an older Russian SNiP seismic load definition is created and the option 'SAVE' is selected, then if the seismic definition is changed to the newer Russian code, the SAVE option is removed as this is not available in the newer code. This would have been reported as an error when the file is next read back.
B) 18 The member query dialog has been updated to display the value of effective concrete width defined for wide flanged members including a composite action as given in the CW parameter.
B) 19 The GUI has been updated to ensure that if the command to report the Member Properties has been included, the command is inserted into the appropriate location in the STD file when the file is created/updated.
B) 20 The GUI has been updated to allow the text in the SET dialogs displayed from the Commands>Miscellaneous> menu folder be localised with a suitable language packs.
B) 21 A number of GUI items have been reformatted to allow their text to be localised with future language packs.
B) 22 The Eurocode combination generator has been updated with a method option which allows the combinations to be created as repeat loads in a new set of primary load cases or alternatively as before in a set of combination cases.
B) 23 The response spectrum loading definition in the loading dialog has been updated for the IBC 2006/ASCE 7-05 definition to ensure that changing the site class does not revert the values of Fa and Fv back to their default values.
B) 24 The database of Jindal steel profiles has been updated to reflect their current section range for ISMC and UC shapes.
B) 25 The text editor has been completely re-designed and enhanced with Intelisense capabilities to assist creating commands, context sensitive help, data grouping/collapsing to assist in manipulating the data, direct links to the section profile tables to assist in selecting profiles and a contents panel for rapid access to relevant locations in the file.
B) 26 The calculation of section properties of General section properties defined with profile points has been improved where previously some sections could not be resolved and would result in the analysis crashing.
B) 27 The Analysis/Print Commands dialog has been updated for the Nonlinear Analysis option to allow the displacement limit node target to be removed and the command line created split if required if it exceeds the line limit.
B) 28 The GUI has been updated to remove BS8110 concrete design from the batch processing. Concrete design to this code should be performed using the Concrete Mode.
B) 29 The Pushover Load dialog in the Loads & Definitions page has been updated to ensure that when a definition of a Displacement Tolerance is created or edited, that setting is correctly assigned to the input file.
B) 30 The GUI has been updated to handle the assignment of FLOOR Loads to a group that has not been defined and report this as an error when opening a file with such a command. Previously, it would remove that command and any subsequent data if the file is re-saved.
(C) Issued Addressed in the Post-Processing Mode (09)
C) 01 The Unity Check table in the Post Processing> Beam>Unity Check Page has been updated to allow the data to be copied to the clipboard and pasted into documents such as Word and Excel.
C) 02 After performing a dynamic time history analysis, the results for displacement, velocity or acceleration can be saved for a selected node. The values for the velocity can now be set using the unit selected from the View>Options>Force Units.
C) 03 The Post Processing Mode has been updated to ensure that the results of Russian steel designs are displayed with the same summaries as reported in the output file.
C) 04 The Steel Design Unity Ratio table has been updated so that if the table is sorted by clicking on column heading, clicking on the sorted row will highlight the corresponding member in the graphics window.
C) 05 The results of the AISC 360 design displayed in the Member Query dialog has been updated to reflect the current Base Unit settings as defined in the Configuration dialog.
C) 06 The Floor Vibration Tool has been updated to corrected to ensure that the values used for the materials are converted to and reported in the correct units. Also a more generic method for calculation for Ec is now used based on the method defined in the AISC Design Guide 11.
C) 07 The Indian steel design IS 800-2007 has been updated to ensure that if slenderness option has been turned off with the MAIN parameter, then it is not displayed in the Steel Design page of the member query dialog.
C) 08 The Member Query dialog has been updated to correct the displayed self weight results for members that have been assigned with a fire proofing system. Previously this would evaluate the applied loading based on the CFP specification instad of BFP, hence the incorrect diagrams. However, note that the diagrams and results elsewhere in the main application were unaffected by this issue.
C) 09 Post processing of prismatic sections where, on top of the basic dimensions YD and/or ZD, the section properties have been defined in the input file, have been updated for reporting the stresses in the Beam>Stresses page.
(D) Issues Addressed in the Steel Design Mode (00)
(None)
(E) Issues Addressed in the Concrete Design Mode (06)
E) 01 The concrete column design to the Russian SP52 design code has been updated to ensure that if the column is subjected to a tensile load case, then the design will cease with a message that columns are currently not designed for tensile cases.
E) 02 The detail report for a Eurocode 2 beam design shear details. The Max allowable transverse spacing between shear legs would show no value and the largest actual transverse spacing between shear legs would display some enormous value. The actual design status would however be reported correctly as OK or Fail.
E) 03 The Eurocode 2 EN1992-1-1 calculation of minimum reinforcement has been updated to ensure that...
E) 04 The design of beams to EN1992-1-1 has been updated to ensure that where the beam is subject to only sagging moments (such as a simply supported beam), then the minimum (hogging) moment that should be considered in the span is not extended to the full length of the beam. Additionally the reported minimum area of tension reinforcement and shear links has been corrected.
E) 05 The Canadian Concrete code CSA A23.3-10 has been updated to correct the minimum prescriptive requirements for transverse spiral reinforcement in columns.
E) 06 The Concrete Design module has been updated to improve the member property reading routines which caused some models to cause STAAD.Pro to crash when opening the file with design results into the Concrete Design Mode.
(F) Issues Addressed in the RAM Connection Mode (01)
F) 01 The design of steel connections to the Bent Plate (BP) templates for Beam Girders (BG) has been updated to ensure that the test for the in plane angle s between 5 and 45 degrees. Previously this had been limited to 15 degrees.
(G) Issues Addressed in the Advanced Slab Design Mode (00)
(None)
(H) Issues Addressed in the Piping Mode (00)
(None)
(I) Issues Addressed in the Editor, Viewer and other modules (18)

I) 01 The Section Wizard application has been updated to support systems which require configuration files to be hosted away from the application folder.
I) 02 The calculation engine in FreeSketch has been re factored to provide a more robust solution algorithm to determine the section properties of the defined profile using the method from the Bentley Structure Property Catalog.
I) 03 The help documentation for Section Wizard and Advanced Mesher have been updated to the CHM format which is more compatible with current operating systems.
I) 04 The method of calculation of the shear centre in the FreeSketch module has been improved.
I) 05 The routine implemented to calculate the plastic modulus values Wplu and Wplv in FreeSketch which were incorrectly based on the elastic axes have been corrected to use the equal area axes.
I) 06 The DXF import routine in FreeSketch has been improved such that any curve or circular lines are subdivided as per the specification in the Preferences dialog.
I) 07 The FreeSketch module has been updated to improve the scope of profiles for which it can report the torsional modulus It.
I) 08 The Equal Area axes used to calculate the plastic section properties are now included in the FreeSketch report. Note that previously these were only reported in the Section Builder module.
I) 09 The calculations of plastic properties have been completely restructured and reported correctly about the equal area axes in both FreeSketch and Section Builder .
I) 10 The GUI has been updated to include an option to display the analysis log file (*.log) created during the analysis process and located in the model folder. This is accessed from the File menu > View > Analysis Log.
I) 11 The legend on the influence surface diagram has been updated to show not only the percentage but also the actual magnitude of the effect based on the application of a unit load at each location across the model.
I) 12 The STAAD.foundation module included with STAAD.Pro has been updated to use XSXML 6 to avoid a known security risk with the earlier versions of XSXML.
I) 13 The CIS/2 module has been enhanced to support the import and export of pipe sections that are not defined in a published catalogue but instead simply defined with external and internal diameters. Previously these section properties would have been omitted from the STP file on export and STAAD.Pro model on import.
I) 14 The ISM creation routines have been updated to allow models to be created with alternative unit formats, such as where the regional settings use the comma as a decimal marker.
I) 15 The STAAD.Pro User Table export from the Section Builder module in Section Wizard has been modified to set the shear areas to 0.0 rather than simply using the cross sectional area which was done previously.
I) 16 The values of torsional modulus IX and warping constant HSS that are exported to a STAAD.Pro User Table have been rewritten to produce more accurate values for a wider range of profiles where previously the calculations resulted in negative values for these properties.
I) 17 The export of a profile in Section Builder to a STAAD.Pro User table has been modified such that the values of shear area are now set to 0.0 as previously they were set to an un-conservative value of Ax. This needs to be set to a manually determined value by the user.
I) 18 A new modelling mode 'Building Planner' has been added to STAAD.Pro specifically to create concrete building models that can be designed with the RCDC Design application. (Note separate licenses are required to activate the Building Planner)
(J) Issues Addressed in OpenSTAAD (02)
J) 01 A duplicated copy of the OpenSTAAD manual has been removed from the installation. The relevant copy is retained in the Help folder.
J) 02 Three new OpenSTAAD functions have been added to access the data of the profile definition of GENERAL USER TABLE sections that include profile points. GetProfileBoundaryInformation(LONG tableNo,STRING 'profile name',LONG nOuter,LONG nInner). The return value is a BOOLEAN that indicates that the profile exists and the number of inner and outer boundaries defined. LONG nPOINTS = Property.GetProfileNoOfPoints(LONG tableNo, STING 'Profile name', BOOL IsInner, LONG nIndex) returns the number of points on a boundary. For the outer boundary, IsInner should be set to FALSE and nIndex set to 0. For an inner boundary, then IsInner should be set to 1 and nIndex should be the index number of the inner boundary. Finally, Property.GetProfileBoundaryPoints(LONG tableNo, STRING 'Profile Name', BOOL IsInner, LONG nIndex, DOUBLE ZP(), DOUBLE YP()) for the given tableNo, Profile Name and boundary the two array ZP() and YP() are filled with the ordinates of the profile points.
(K) Issues Addressed with Documentation and Printing (20)
K) 01 The User Report has been updated to ensure that the detail of members designed to the AIJ code matches the format of the report included in a standard output file.
K) 02 Details of the command DESIGN ELEMENT has been added to the International Design codes section 11.A Indian Codes - Concrete Design per IS456.
K) 03 The Technical Reference manual section 5.5 SET Command has been updated to provide more detail on the SET FLOOR LOAD TOLERANCE provisions.
K) 04 The Russian steel design parameter values for SGR have been corrected.

K) 05 Details of the OpenSTAAD function IsAnalysing has been added in the OpenSTAAD manual
K) 06 Chapter 5.31.2.3 Colombian NSR-98 Seismic Load has been updated with a correction to the equation of Cvx.
K) 07 Section 5.40 of the Technical Reference manual, Load Envelope has been updated with details of the various envelope classifications.
K) 08 The Russian Steel design manual for SP 16.13330.2011 has been updated to clarify the use of Russian and European steel sections in a design.
K) 09 Details of the function GetBeamSectionPropertyRefNo has been OpenSTAAD manual.
K) 10 The descriptions of KY and KZ have been updated in section 2.3.4 of the Technical Reference manual to clarify that these terms are 'about' the local axis.
K) 11 Correction of CMN list in old Russian steel SNiP code
K) 12 The examples of a number of OpenSTAAD functions have been updated to remove parentheses which should not be used where functions are not returning a value.
K) 13 The Technical Reference manual section 5.32.12.2.1 Generation of UBC or IBC Seismic Loads, has been revised with more information about the optional torsional forces that can be generated.
K) 14 Section 1.18.3.2 Mass Modelling has been updated to clarify possible effect of including CON member loads on the mass matrix.
K) 15 The technical details of Master/Slave settings have been updated to clarify that due to the mechanisms used to include master/slave systems, if the reactions on master nodes are not included in a statics check and can result in an out of balance report. This can be avoided by adding a short stiff member from a master node to the support.
K) 16 Details of 4 dynamic functions have been added to the OpenSTAAD manual.
K) 17 The Technical Reference Manual section 5.32.10.1.2 Response Spectrum Specification in Conjunction with the Indian IS: 1893 (Part 1)-2002 has been updated and to clarify the specification of torsional requirements.
K) 18 Section 13.6 of the Graphical User Interface manual has been updated to confirm that when launched from within a STAAD.Pro session, the use of Section Wizard does not require an additional license and hence is a free module in STAAD.Pro.

K) 19 The online help documentation for the SAX Macro Editor has been updated to support the methods used in the current Windows operating systems.
K) 20 Sections 5.25 Member Offset Specification and 5.26.2 Specifying Constants for Members and Elements of the Technical Reference manual have been updated to clarify that 'Local offsets are defined in the local axes prior to rotation when a BETA angle is used.'
(L) Issues Addressed with licensing / security / installation (03)
L) 01 The icons in the License Configuration Panel on the Start Screen have been updated to ensure that they display the appropriate status if turned off. Whilst the program behaved correctly, there were times when rather than displaying a grey icon and unset, the application would show a red icon and a check next to the item. Restarting the program would display the correct status.
L) 02 The warning that is reported in the output file when the applied vertical load is less that the self weight has been reformatted to ensure that it fits in a standard page and does not generate a warning when being printed.
L) 03 The files in the European samples folder EXAMP/EUR have been updated to refer to the current Eurocode for steel design and use European sections where appropriate.
JavaScript must be enabled in order to use this site.
Please enable JavaScript in your browser and refresh the page.
This section contains details of the STAAD.Pro commands used to create STAAD input files which are read by the STAAD engine.
Introduction
The STAAD.Pro graphical user interface (GUI) is normally used to create all input specifications and all output reports and displays. These structural modeling and analysis input specifications are stored in STAAD input file – a text file with extension, .STD. When the GUI opens an existing model file, it reads all of the information necessary from the STAAD input file. You may edit or create this STAAD input file and then the GUI and the analysis engine will both reflect the changes.
The STAAD input file is processed by the STAAD analysis 'engine' to produce results that are stored in several files (with file extensions such as ANL, BMD, TMH, etc.). The STAAD analysis text file (file extension .ANL) contains the printable output as created by the specifications in this manual. The other files contain the results (displacements, member/element forces, mode shapes, section forces/moments/displacements, etc.) that are used by the GUI in the post processing mode.
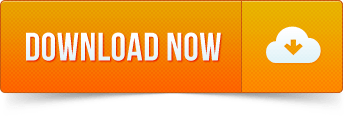